持続可能な社会の実現のため、今後はプラスチックのケミカルリサイクルが普及していくと考えられます。
この記事では、ケミカルリサイクルの中の熱分解油化技術を実用化している企業を紹介します。
プラスチックの熱分解油化技術の実用化は、欧米および日本で実用化が進んでいます。
プラスチックの熱分解油化
プラスチックの熱分解油化は、廃プラスチックを無酸素条件下で加熱分解してナフサなどの熱分解油を製造する方法です。熱分解油はナフサクラッカーに投入してエチレンなどの基礎化学品に変換されます。
プラスチックの熱分解油化では、炭化水素系プラスチックであれば、PE、PP、PS等の混合プラスチックでも処理することができます。ただし、酸素原子を含むPETや塩素原子を含むPVCは設備の腐食の原因になるため処理前に除去します。熱分解油化では熱分解油のほかにガスや高沸点残渣も生成し、熱分解油の収率が低いことが課題です。
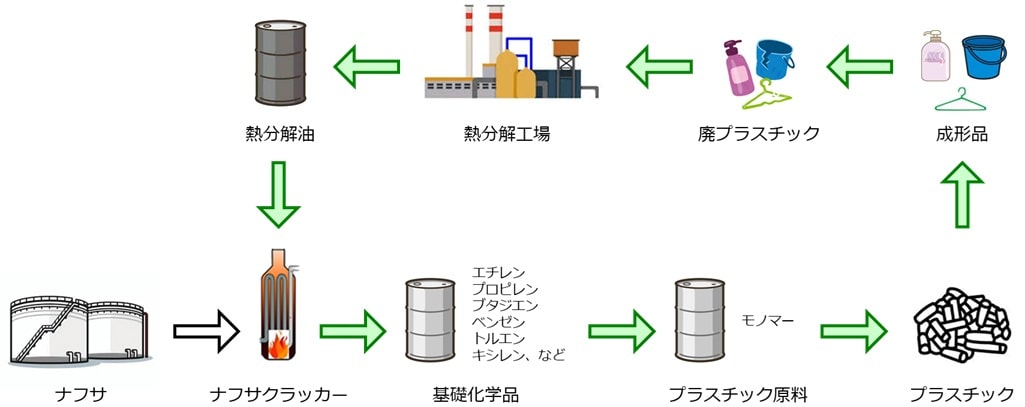
プラスチックの熱分解油化を実用化している企業
現在稼働中(および計画中)の熱分解油メーカーを表にまとめました。
熱分解油 メーカー | 工場所在地 | 稼働開始 | 処理能力 万トン/年 | 提携石油化学 メーカー | |
Plastic Energy | Almeria | スペイン | 2016 | 0.5 | Total |
Seville | スペイン | 2017 | 0.5 | Total | |
Le Havre | フランス | 未 | 3.3 | ExxonMobil | |
Geleen | オランダ | 未 | 2 | SABIC | |
Grandpuits | フランス | 未 | 1.5 | Total | |
Pryme | Rotterdam | オランダ | 2023 | 4 | Shell |
Mura Technology | Teesside | イギリス | 2024 | 2 | Dow |
Renasci | Ostend | ベルギー | 2020 | 1.8 | Borealis |
BlueAlp | Ostend | ベルギー | 2020 | 7 | Shell |
Quantafuel | Skive | デンマーク | 2022 | 2 | BASF |
Fuenix | Weert | オランダ | 2022 | 2 | Dow |
ARCUS | Frankfurt | ドイツ | 2022 | 0.4 | BASF |
New Hope Energy | Tyler | アメリカ | 2018 | 5 | Total |
Braven | Zebulon | アメリカ | 2020 | 1.2 | Chevron Phillips |
ExxonMobil | Baytown | アメリカ | 2022 | 4 | ExxonMobil |
Alterra energy | Akron | アメリカ | 2022 | 2 | Neste |
Nexus Circular | Atlanta | アメリカ | 2023 | 1.4 | Braskem、Shell |
歴世礦油 | 新潟 | 日本 | 1996 | 0.6 | – |
三菱ケミカル、ENEOS | 鹿島 | 日本 | 未 | 2 | 三菱ケミカル、ENEOS |
ケミカルリサイクルジャパン | 市原 | 日本 | 未 | 2 | 出光興産 |
LG Chemical | Dangjin | 韓国 | 未 | 2 | LG Chemical |
SK Geo Centric | Ulsan | 韓国 | 未 | 6.6 | SK Geo Centric |
Plastic Energy
Plastic Energyは2011年に設立され、ロンドンに本社を置いています。Almeria(スペイン)とSeville(スペイン)にリサイクル工場をもち、さらに3工場を建設予定です。
Plastic Energyは、プラスチックを炭化水素ガスに変換してからTACOILと呼ぶ熱分解油にリサイクルする、独自のTACプロセスを開発しています。このTACプロセスは複数の企業にライセンスされ、世界中でプラスチック廃棄物をリサイクルするために使用されています。
TACプロセスの概要
- プラスチック加熱して融かします。
- 溶融したプラスチックを反応炉に送り、酸素がない状態でさらに加熱して分解させ、ガス化します。触媒は使用しません。
- 得られた炭化水素のガスは分離精製され、熱分解油(TACOIL)となります。
- 熱分解油は、石油化学パートナーへ販売されます。
TACプロセスのライセンス企業
- SK Geo Centric:2023年にライセンス契約。韓国の蔚山にリサイクル工場建設予定。
- NOVA Chemicals:2023年にオンタリオ州にリサイクル工場を建設する可能性を調査する契約を締結。
- INEOS Olefins & Polymers Europe:2022年に処理能力10万トンの工場建設に関する契約を締結。
- PETRONAS Chemicals Group:2023年にリサイクル工場を建設するための最終投資決定に達しました。
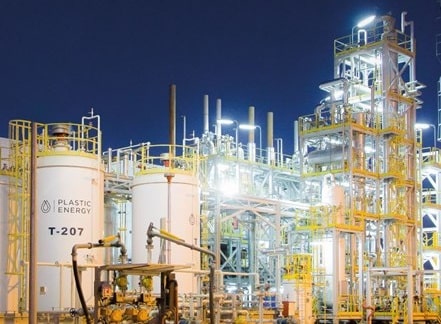
Pryme
Prymeの創立者は2008年からプラスチック廃棄物のケミカルリサイクルの研究をはじめ、2023年にRotterdamに最初のリサイクル工場を稼働させました。Prymeの開発したプロセスは、プラスチック廃棄物から熱分解油への変換効率が高く、大スケールに対応でき、二酸化炭素排出量が少なく、低コストです。Prymeの熱分解プロセスは、熱分解油の高沸点留分の一部を熱分解炉に再投入することが特徴です。
Prymeの開発した熱分解プロセスの概要
- プラスチック廃棄物を短時間(30秒)で300℃に加熱して水分と低沸点成分や塩素成分を除去しながら、押出機で熱分解炉に5トン/時で供給する。
- 600℃まで加熱可能な電気加熱式の熱分解炉で、無酸素条件で熱分解する。
- 最適な温度制御によりプラスチック廃棄物中の有機物は100%分解される。
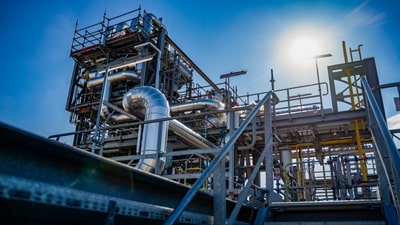
Mura Technology
Mura Technologyは2016年に設立され、2024年にTeesside に2万トン/年の処理能力のリサイクル工場を稼働させました。Mura Technologyは、プラスチック廃棄物を高温高圧の超臨界水を用いて分解する、独自のHydro-PRTプロセスを開発しています。三菱ケミカルとLG ChemicalにMura Technologyの技術をライセンスしています。
Hydro-PRTプロセスの概要
Mura Technologyの熱水リサイクルプロセスであるHydro-PRTは、超臨界水を使用してプラスチック廃棄物を熱分解油に変換し、新しいプラスチックの原料へとリサイクルします。
Hydro-PRTプロセスのライセンス企業
- 三菱ケミカル:2021年にライセンス契約。2024年に2.5万トン/年の処理能力のリサイクル工場を建設する予定。
- LG Chemical:2021年にライセンス契約。2.5万トン/年の処理能力のリサイクル工場を建設する予定。
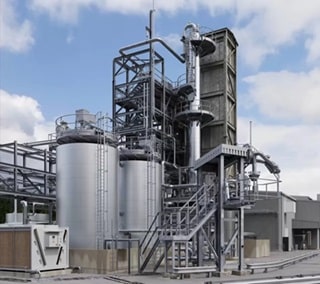
Renasci
RenasciのOstendにあるリサイクル工場では、RDF(廃棄物由来燃料)とプラスチック廃棄物を処理できます。それぞれの処理能力は、RDFが10.2万トン/年、プラスチック廃棄物が1.8万トン/年です。
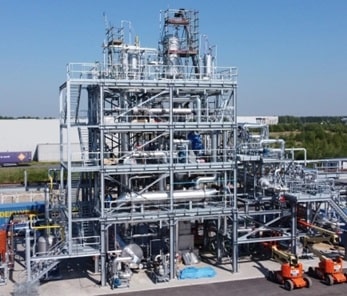
BlueAlp
BlueAlpは2014年にパイロットプラントを建設して6年間試作を続け、2020年に2.5万トン/年の処理能力を持つ商用プラントを建設しました。さらに2022年には生産能力を7万トン/年に増加させました。BlueAlpは自社技術のライセンス先を募集しています。
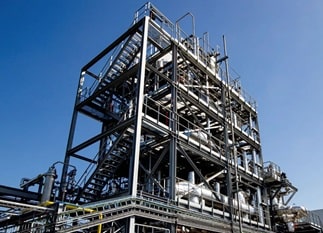
Quantafuel
Quantafuelは2007年から研究開発を開始し、2014年にメキシコにパイロットプラントを建設し、様々な種類のプラスチックをケミカルリサイクルする技術を確立しました。そして2022年にデンマークのSkiveに2万トン/年の処理能力を持つ商業プラントを建設しました。Quantafuel の熱分解では触媒を使用して付加価値の高い炭化水素が豊富な熱分解油を製造しています。
Quantafuel は2024年に廃棄物処理およびエネルギー回収の大手企業Viridorの子会社になっています。
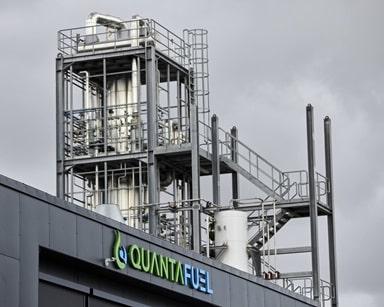
Fuenix
FuenixはSulzerの子会社です。2018年からオランダのWeertにあるリサイクル工場を稼働させ、徐々に処理能力を拡張しており、2022年からは2万トン/年の処理能力を有しています。
Fuenixの開発した熱分解プロセスは、高効率で設備投資額が抑えられる特徴があります。Fuenixはライセンスを通してプラスチックのケミカルリサイクルを世界に広げたいと考えています。
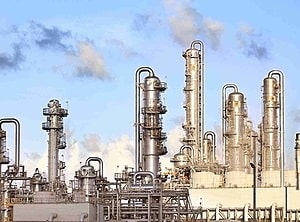
ARCUS
ARCUSは2017年に設立されました。ARCUSはFrankfurtにあるリサイクル工場でプラスチック廃棄物を熱分解し、Arcus Liquidと呼ぶ熱分解油を製造しています。
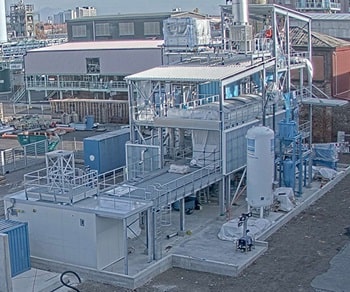
New Hope Energy
New Hope Energyは2018年にアメリカのTylerで5万トン/年の生産能力を持つリサイクル工場を稼働させました。
Lummus Technologyは、2020年に商業的に稼働している世界中の熱分解プラント26社をレビューしました。その結果、New Hope Energyは、熱分解油の生成率の高さ、商業的な運用、技術の拡張性、および製品純度の面から、最高と評価されています。
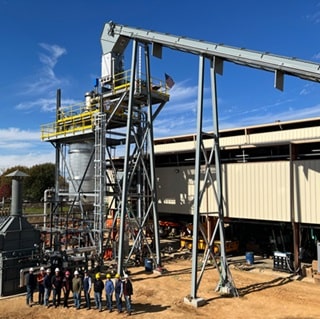
Braven
Bravenは2020年にアメリカのZebulonで1.2万トン/年の生産能力を持つリサイクル工場を稼働させました。Bravenの熱分解油はBraven PyChemと言う商標名で、Chevron Phillips Chemicalに販売され、クラッキングされています。
Bravenは、同社の熱分解システムを利用するプラントを立ち上げるパートナー企業を募集しています。Bravenのシステムはモジュール化されており、1年以内の短期間で稼働させることができるそうです。
ExxonMobil
ExxonMobilは2022年にBaytownで4万トン/年の生産能力を持つリサイクル工場を稼働させました。ここで製造される熱分解油は、自社のクラッカーで基礎化学品にされ、マスバランス方式を利用して、循環型プラスチックを手掛ける顧客向けにExxtendという商品名で販売されています。ExxonMobilの熱分解プロセスは、炭化水素溶媒を使用することが特徴です。
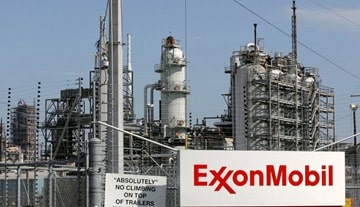
Alterra energy
Alterra energyは2020年にアメリカのオハイオ州Akronで2万トン/年の生産能力を持つリサイクル工場を稼働させました。Alterra energyの開発した熱分解プロセスでは、PVC(塩ビ)を含むプラスチック廃棄物を処理することも可能で、さらに熱分解で得られるすべての成分を有効に利用することができます。Alterra energyはライセンスを通してプラスチックのケミカルリサイクルを世界に広げたいと考えています。
Alterra energyの開発した熱分解プロセスの概要
- 細断されたプラスチック廃棄物をホッパーに落とし、コンベアベルトがそれを押出機に運びます。
- プラスチック廃棄物は押し出し機の中で加熱され、均一な密度になります。
- プラスチック廃棄物は、PVC(塩ビ)から塩素を除去するために酸化カルシウムと混合され、約80%の塩素が除去されます。(塩素が熱分解油に残っていると、下流の顧客の化学製品製造設備を腐食・損傷させる可能性があります)
- 熱分解反応器内では、プラスチック廃棄物が無酸素状態で約400~550℃で加熱され、長いポリマー鎖が、炭素数が3(C3)のガスから炭素数が30(C30)程度のワックスへと熱分解されます。
- 熱分解反応器はゆっくりと回転して内容物を混ぜ、重力で液体が流れ続けるように下向きに傾けられています。
- 熱分解油は石油化学会社に送りクラッキングされ、ガス成分は熱分解炉の加熱用燃料として使用され、有機物と塩化カルシウムが混合された残渣はアスファルト原料として利用されます。
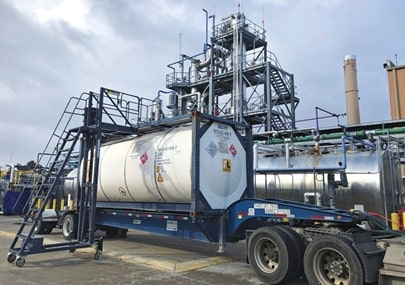
Nexus Circular
Nexus Circularは2023年にアメリカのAtlantaで1.7万トン/年の生産能力を持つリサイクル工場を稼働させました。さらに、2025年、2026年にそれぞれ8.1万トン/年の生産能力を持つリサイクル工場を稼働させる計画をしています。Nexus Circularのプロセスでは、HDPE、LDPE、PP、PS の4種類のプラスチック廃棄物を処理することができ、熱分解油(82%)、炭化水素ガス(13%)、残渣(5%)が生成します。
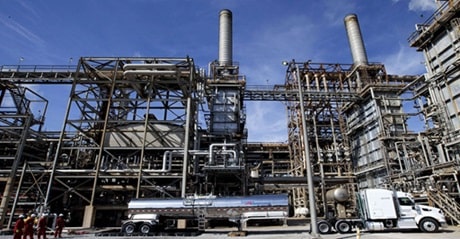
歴世礦油
歴世礦油では、新潟市の一般家庭から出るプラスチック廃棄物を塩ビも含めてそのまま混合処理する新潟資源リサイクルセンター(旧 新潟プラスチック油化センター)を1996年から稼働させています。新潟資源リサイクルセンターの熱分解では、プラスチック廃棄物から軽質油を約30%とA重油相当の油を約30%が得られます。軽質油は施設内の加熱炉などで自家消費され、A重油はA重油の用途で使用されます。そのため、プラスチック廃棄物の熱分解ですが、再びプラスチックに戻るリサイクルではありません。
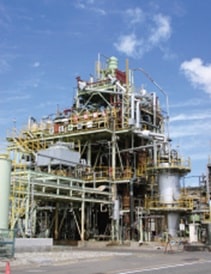
三菱ケミカル、ENEOS
三菱ケミカルとENEOSは、共同でプラスチック廃棄物のケミカルリサイクル事業を立ち上げています。
両社はMura Technology社のHydro-PRT技術を導入し、プラスチック廃棄物を高温・高圧条件下の水(超臨界水)で熱分解してナフサを製造し、両社の既存のナフサクラッカーに投入して、エチレン、プロピレン、ベンゼンをはじめとした基礎化学品とその誘導品を生産します(三菱ケミカルプレスリリース)。

ケミカルリサイクルジャパン
ケミカルリサイクルジャパンは出光興産の子会社です。2024年に市原において熱分解プラントの建設を開始しました(出光興産ニュースリリース)。
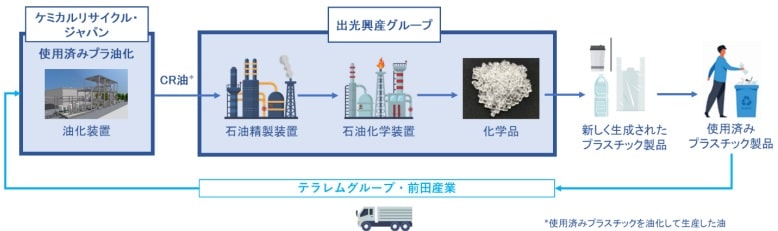
LG Chemical
LG Chemicalは2023年に韓国のDangjinにおいて熱分解プラントの建設を開始しました(LG Chemical blog)。LG ChemicalはMura Technology社のHydro-PRT技術を導入します。
SK Geo Centric
SK Geo Centricは2023年に韓国のUlsanにおいて熱分解プラントの建設を開始しました(SK Geo Centric News)。SK Geo CentricはPlastic Energy社の技術を導入します。
まとめ
この記事では、ケミカルリサイクルの中の熱分解油化技術を実用化している企業を紹介しました。
プラスチックの熱分解油化技術の実用化は、欧米および日本で実用化が進んでいます。
持続可能な社会の実現のため、今後はプラスチックのケミカルリサイクルが普及していくと考えられます。
関連書籍
本書はプラスチックのリサイクル技術を網羅的に解説しています。廃プラスチックリサイクル技術概論から始まり、マテリアルリサイクルとケミカルリサイクル技術の開発動向と応用展開、プラスチック包装材料に関わる国内外の法規制、廃プラスチックリサイクルにおける要素技術の開発動向など、幅広い内容です。個人で購入するには高額な本です。プラスチックのリサイクルに事業として取り組む方におすすめです。
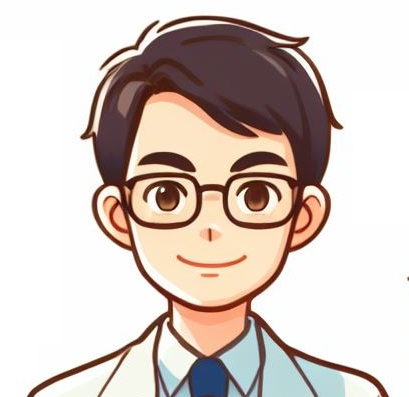